Find the answers to the questions we get asked the most. If you can't find what you're looking for here please don't hesitate to contact us.
Drive Showers FAQ's
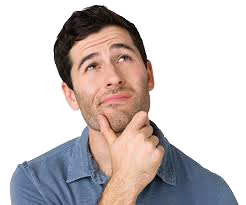
- Do I need a drive shower?
According to the certified MerCruiser Master Technician that Simrek contacted, "every boat should have a drive shower." There are two obvious signs that your drive may be running TOO HOT:
A. If there is a continuous need to remove a white chalky deposit from the top half of the stern drive. The white chalky deposit means that the outside casing of your drive is running hot enough to boil off the water that is splashed onto it. This boiling process turns the water into steam and leaves the mineral deposits behind to bake onto your drive. The hotter the drive, the more deposits are collected, and the harder they are to remove.
B. Other signs that your drive may be running too hot include paint discoloration, or a cloud of steam that appears every time your boat comes off plane. Unless you have opened through hull exhaust, what you are seeing is not exhaust; it's the steam that is generated when a hot drive is plunged into cool water. This process of heating and rapid cooling is known as thermal shock and can be detrimental to metal components, especially aluminum, if the range is extreme enough. Keep in mind that however hot the casing is, the components inside are running much hotter. Published test results show that some stern drives components operate in excess of 350 degrees. If you are experiencing any or all of the above conditions, your drive is probably operating over 250 degrees. For the same reasons that automotive engineers established approximately 200 degrees as an optimum operating temperature for their engines, most marine experts agree that this also holds true for stern drives.
Drives listed in order by operating temperatures:
(hottest)
Bravo III (270+ degrees)
Alpha (all) 265+ degrees
Bravo II
Bravo HP, XR and ZR Drives (due to their performance applications)
Bravo I
(coolest)
- What does a drive shower do?
Drive showers distribute a continuous supply of cool water to the top portion of the stern drive. Tests have shown that cooling like this can double the bearing life and service life of the drive oil by lowering an operating temperature of 220 to 350+ degrees Fahrenheit a minimum of 30%. It prevents oil foaming, the primary cause of oil break-down which can lead to drive failure. It also dramatically reduces the thermal shock that occurs when the hot drive is plunged into cool water every time the boat comes off plane. These conditions exist on nearly every boat, but is especially prevalent in a high performance application where demands on the drive are pushed to the limit. Under normal operating temperatures, most manufactures recommend that the oil in their drives be changed every 50 hours. For some, 50 hours can be a few week's worth of use.
- What is thermal shock?
This is a condition that exists when metal, or other materials, are heated up and then cooled quickly. The materials expand from the heating process and contract rapidly when cooled. The drive casing is made of cast aluminum which can develop small stress cracks when subjected to thermal shock on a frequent basis. Also, the many bearings and gears inside the drive develop excess wear from the constant dimensional changes that occur during thermal induced expansion and contraction.
- Why a Multiport Drive Shower®?
The Simrek Multiport Drive Shower® System utilizes two of the most efficient pick-up ports possible for more than twice the water volume than any other drive cooling system available. It is also the most efficient because it targets the top and two sides of the drive. All the other cooling systems available target only one surface of the drive with one dump port. Drive shower systems that only spray water on top of the drive are less efficient because they target the bearing cap on the top of the drive which is over an inch thick. The sides of the drive are less than 1/8th of an inch thick and offer much less resistance to temperature change.
- What about other drive showers?
There are two designs of shower systems targeting the top bearing cap. One is a solid tube design, the other is a flexible tube design with and without a bearing cap plate. At first glance, both would appear to cool the sides of the drive simply because the water will run down from the top. Consider these two conditions:
The solid tube system sprays water at the top surface of the drive from a 1/2 inch diameter tube which is located at a 90 degree angle to the top of the drive, and about 1/2 inch away. Try this experiment at home: turn a drinking glass up side down, and hold it under your faucet approximately 1/2 inch away. Now turn the faucet on full force. You will probably find that every thing in the room is now soaking wet, (including yourself --- sorry about that!), except the sides of the glass are still dry. This is due to the force and velocity that the water is under as it exits the faucet. The same principles hold true in the case of a drive shower.
The flexible tube system with an optional bearing cap plate directs the water at the top bearing cap at almost a 180 degree angle. This causes the water to skip over the top of the drive and exit out the back of the plate on to your transom. This is a great way to wash your transom, but not a very efficient cooling system for your drive. Try this experiment at home: turn a kettle up side down in your drive way. (This time I promise you that you won't get wet.) Hold a garden hose, at an angle a little more than horizontal to the ground and about an inch away from the kettle. Open the spray nozzle to full force. You will probably find every thing behind the kettle is soaking wet, but the sides of the kettle are still dry.
With the force of the water that is traveling through a 1/2 inch diameter tube at speeds equal to the that of the boat, it is easy to see that this water will only go where it is aimed, and gravity will have little influence on its path. Through the use of multiple dump ports aimed at the top and both sides of the drive, the Simrek System delivers the cooling water under less pressure, which allows it to spend more time in direct contact with the side surfaces of the drive.
- Will the Multiport Drive Shower® cause drag and slow my boat down?
Because the water is only being re-directed, instead of being forced to build back pressure (as it does in the case of a speedometer pick-up) no speed reduction will be noticed. The Multiport Drive Shower® is used on a large number of race boats.
- Will this Multiport Drive Shower® cause cavitation?
The pick-up ports on all of the other drive cooler systems are mounted through the anticavitation plate very close to the top and back side of the propeller. Sometimes at lower speeds, having the pick-up ports close to the back of the propeller can allow it to draw air down the tubes and into the prop stream causing aeration of the water and the propeller to cavitate. Our new Max System locates the two pick-up ports outboard of the anti-cavitation plate away from and in front of the propeller.
- How much cooling water does the Multiport Drive Shower® supply?
At 40 mph, the Multiport Drive Shower® is supplying cooling water to the top half of your drive at a rate of 53 gals./min. or .9 gal./sec. That is approximately four times the flow of your bath tub faucet.